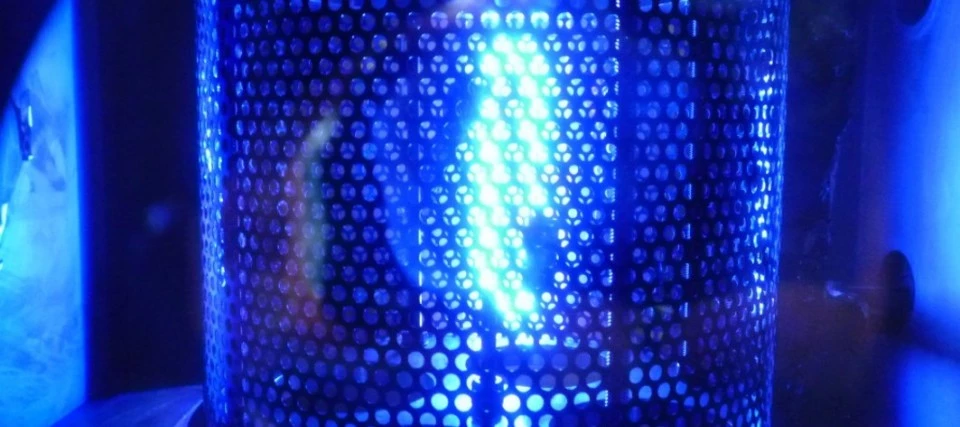
Research group: Surface engineering
Pioneering new products and processes to improve the performance and function of a wide range of materials essential to modern technology.
About
About our research
Surface engineering enables much of modern technology, from electronics, sensors and displays to catalysts, advanced mechanical components and biomedical devices. It provides the often-hidden element essential to many science and engineering products and processes.
Within our research group, we use a range of technologies that can modify the physical or chemical nature of a surface, or grow new materials as thin films on top of components and substrates to alter their function.
We are experts in the development and application of a physical vapour deposition technique known as magnetron sputtering — and are the leading academic exponents of this technique, particularly with the use of pulsed plasmas.
Other techniques we specialise in include vacuum evaporation, chemical vapour deposition, ion beams, plasma surface processing, and atmospheric pressure plasma systems.
Our core activities are:
- production of functional thin films with project specific properties
- characterisation of the physical, structural, optical, catalytic, chemical and tribological properties of thin films
- characterisation and development of advanced deposition processes
Our specialist research areas include:
- physical vapour deposition process development and characterisation
- plasma-enhanced chemical vapour deposition
- atmospheric plasma processing
- barrier layers for packaging applications
- transparent conductors
- nuclear barrier and protective coatings
- photocatalytic coatings for self-cleaning, pollution remediation, antimicrobial, water splitting and chemical synthesis applications
- hygienic and antimicrobial surfaces
- fuel cell and battery coatings
We work closely with the University’s pioneering PrintCity facility and the Manchester Fuel Cell Innovation Centre.
Our facilities
Our work is highly applied in nature, and generally focused on the end use of the particular coating/substrate system.
As well as fundamental academic study, we work on commercial process and product development using our magnetron equipped coating systems on surfaces from 75mm in diameter, up to 380mm x 120mm.
Most of our systems are equipped with more than one source and can be operated in metallic or reactive sputtering modes.
This gives us flexibility in which materials we can deposit — including metals, alloys, ceramics, multi-layers and graded materials — and the size and type of substrates that can coat. As well as planar substrates such as metals, glass and plastics, we also have a bespoke system for coating powders and nanoparticles.
Our facilities include:
- Nine vacuum-based coating systems for PVD and PECVD of up to commercial production capability size, each equipped with a range of state-of-the-art coating technologies
- Atmospheric plasma systems
- A variety of power delivery techniques including microwave, radio-frequency, pulsed-direct current, alternating current and HiPIMS supplies
- Capability to deposit a wide range of metal, alloy and ceramic materials from nanometre range upward onto bulk components, powders and particulates, and polymeric web
- A suite of analytical techniques, including:
- analytical FEGSEM with EDX and micro-Raman
- GIXRD
- XPS
- AFM
- raman spectroscopy and SERS
- optical surface profilometry
- nano-mechanical testing
- tribo-testing
- spectrophotometry
- catalytic and electrochemical analysis
Organisations we work with

The Royal Society

Bobst

National Nuclear Laboratory
Contact
Contact us
You can contact individual members of the team through their staff profiles.
For general enquiries, please contact our research group lead Dr Glen West.